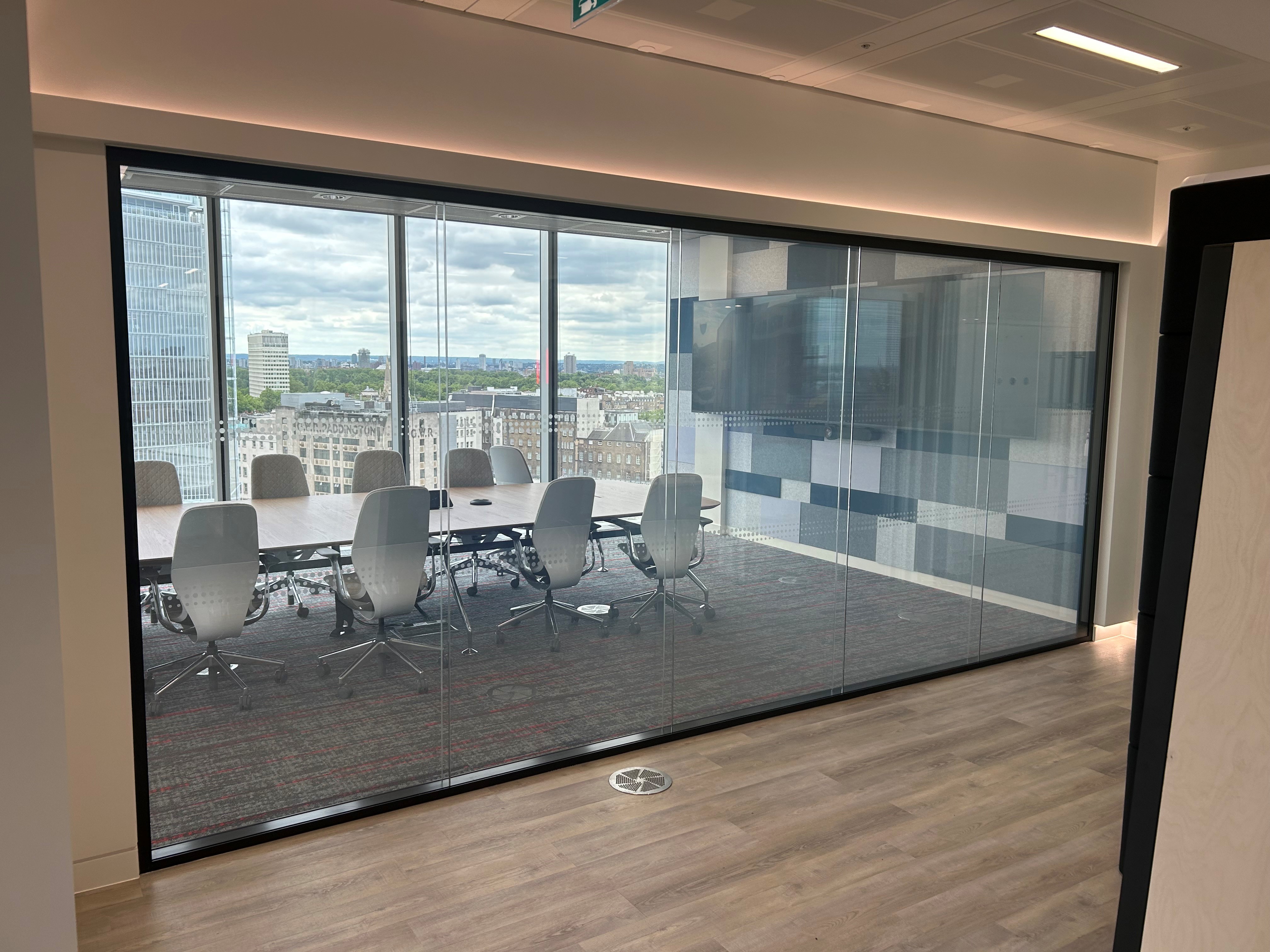
As architects and designers work to design and construct building projects in a more sustainable manner, the consideration of embodied carbon has become a bigger factor in understanding the overall impact of a project’s carbon footprint.
Therefore, we’ve decided to explore the topic of embodied carbon in glazed partitions in this blog.
Most of the embodied carbon in glass originates with the energy-intensive process of heating the melting furnace to 1600 degrees Celsius to convert a blend of silica, soda ash, dolomite, metal compounds and recycled cullet glass to flat glass.
The processes of adding energy-efficient low-e coatings, tempering, laminating and fabricating flat glass into insulating glass units also contribute to the glass’s GWP (Global Warming Potential) – but to a lesser degree.
In fact, approximately 75% of the embodied carbon in a glass unit can be credited to the manufacturing of float glass. It is estimated that of a glass panel’s remaining embodied carbon, 10% comes from the fabrication process itself and just 15% comes from the process of adding low-e coatings and heat treatment processes.
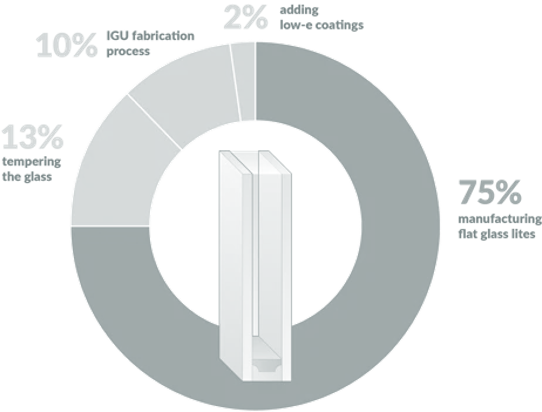
Glazed partitions can have a long life, typically tied into the length of an office lease, though often longer. When specifying partitioning it’s reasonable to expect product lifespans of 20 years or more and being demountable can be re-utilised again and again.
At the end of life, the aluminium or steel extrusions used to make the frames can be recycled, as can door ironmongery. Whilst glass is energy intensive to make (one kg of flat glass uses roughly 25MJ/kg of energy and 1.76kgCO2-eq/kg*) it is also fully recyclable and can be recycled almost infinitely.
If you'd like to discuss embodied carbon in greater detail, contact us here and our expert team will happily assist. Alternatively, we delve into the topic in greater detail in our RIBA-approved CPD, 'Specifying Glazed Partitions. You can sign up for a CPD here.
Related articles
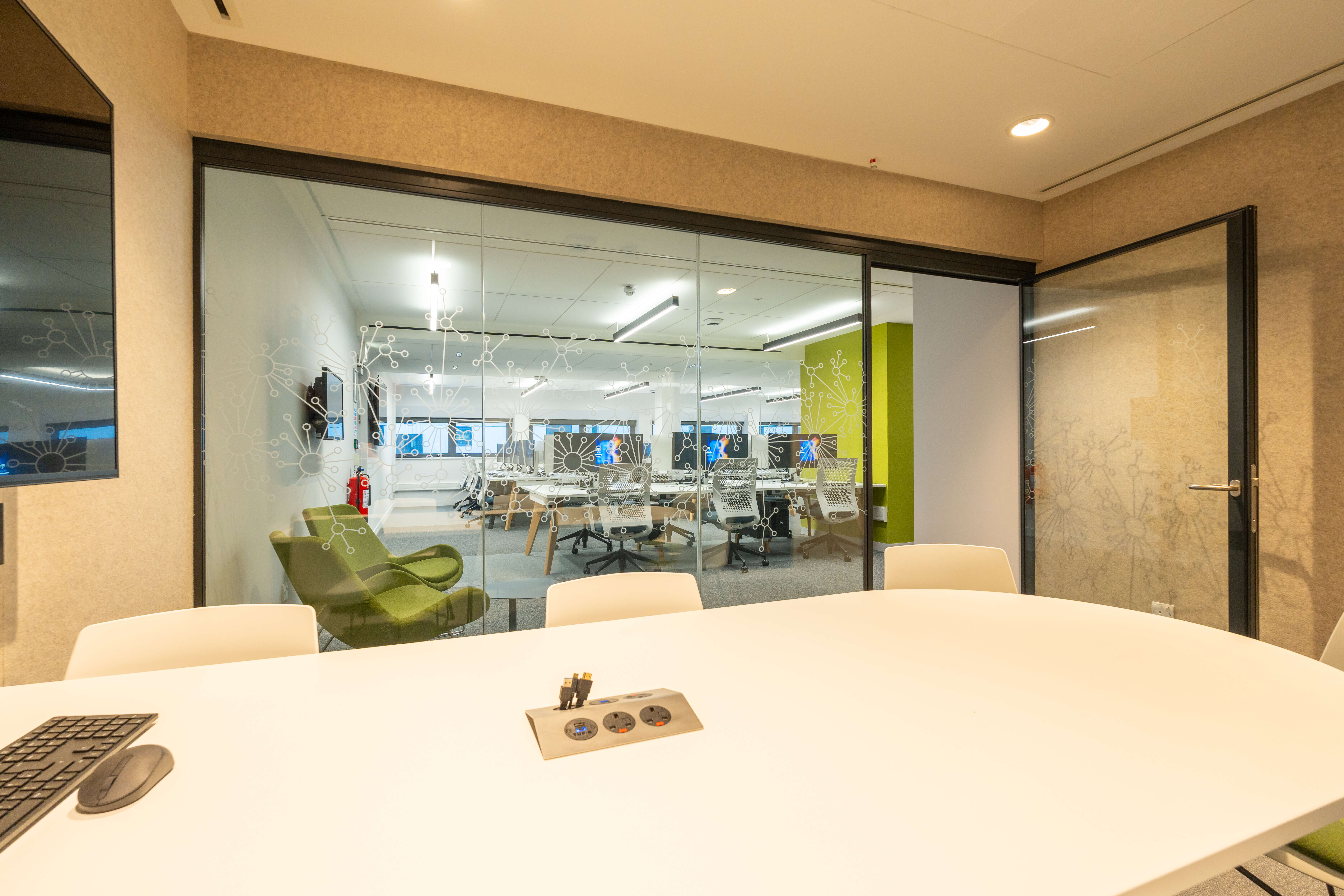
Using acoustic glazed partitions to help achieve WELL certification
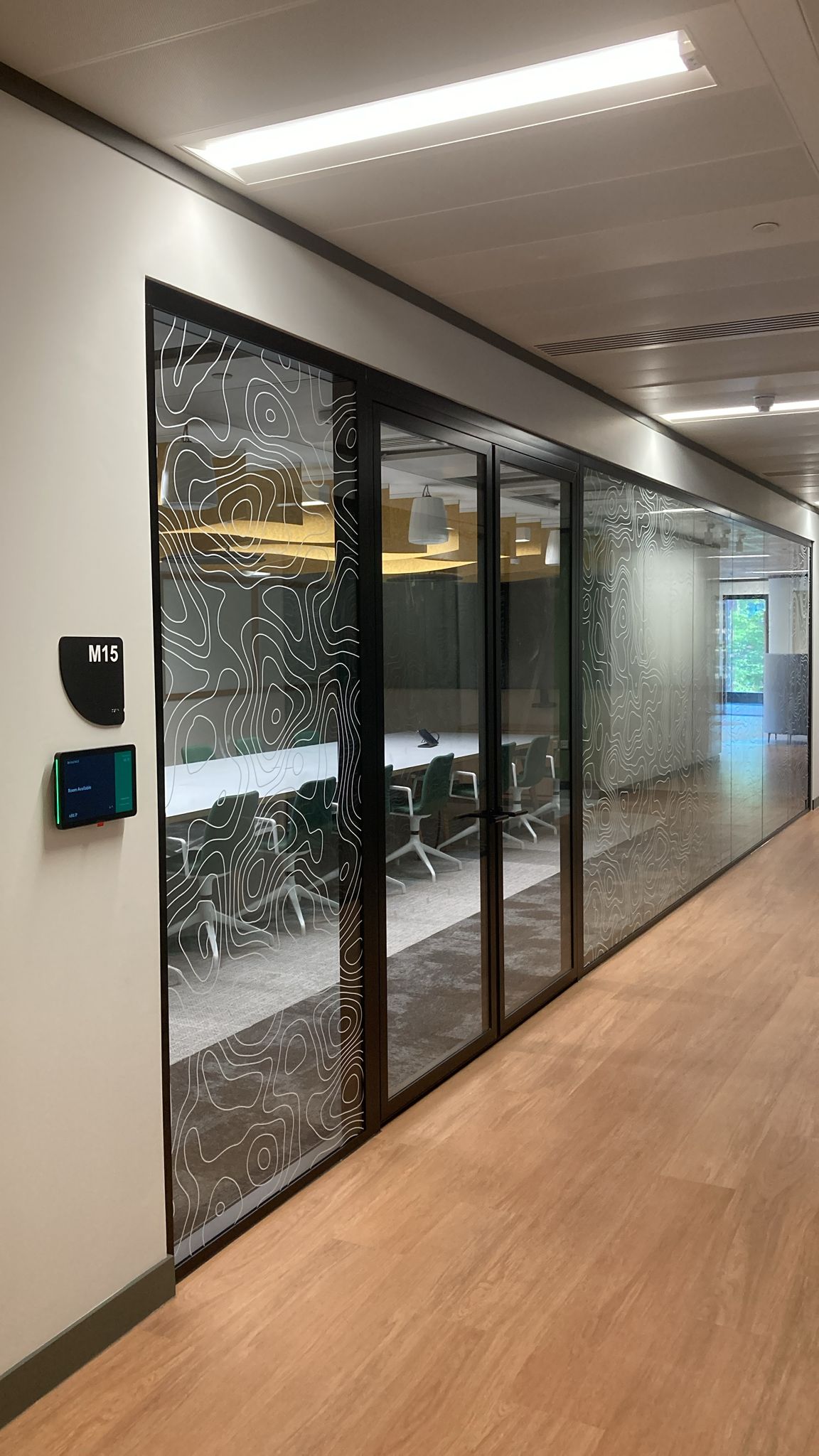